Dr. Daisuke Mizuno: Corrosion and Protection in Automotives

BANDUNG, itb.ac.id – Development of modern materials is a key to advancement in science application for practical use. Modern materials shall bear durability, lightness, flexibility and resistance to the most extreme condition such as resistance to corrosion. Materials used for structures and automotive have to be corrosion resistant in order to continue operating over a relatively long period before the eventual decline.
This topic on corrosion in automotive was brought by Dr. Daisuke Mizuno, a researcher from JFE Steel Japan in joint seminar on Thursday (16/03/17). Taking place in Seminar Room Labtek II FTMD, the seminar brought the theme “Advanced Technology Related to Automotive Steel Sheets”. On his session, Dr. Daisuke Mizuno described common corrosion types on automotive and methods of protection.
Vehicles that have been operating for a particular set of time might endure corrosion, either minor or severe, with cosmetic corrosion and perforation corrosion as two commonly occurred corrosion on vehicles. Cosmetic corrosion, as the name suggest, occurs under the paint layer, specifically on scratches or any other deformation. This corrosion seldom occurs to the latest painting techniques such as inducing electricity to the paint job and the surface of vehicle that make the paint stick to the surface evenly. Perforation corrosion occurs on gaps and pile ups such as under the bonnet and the corners of inner parts of car doors. Both cosmetic and perforation corrosion are affected by the thickness of coating on the surface. On places where snow falls, corrosion may occur because of ice melts that contain salts. Based on a study on corrosion on vehicles, five most-corroded parts on cars are the end and under the bonnet, tip of the trunk, wheel house, side hills and the lower end of the door.
Among many protection methods for automotive against corrosion, the most utilized ones are hot dip galvanizing and electro-galvanizing. Hot dip galvanizing is done by dipping the steel strip continually to molten zinc. This method is popular due to its low cost and thick coating result. Electro-galvanizing is done by electrolyzing Zn-Fe or Zn-Ni. This method cost more because of the electrical power used during the coating.
Hot dip galvanizing is further developed to galvannealed. In this process, metals that have gone through hot dip process are treated with annealing. During this process, the Fe containing the coating is about 7-15 wt%. Galvannealed steel has good productivity and balance in performance. Galvannealed commonly used by Japan manufacturers in response to the demand of the country’s automotive manufacturers while hot dip galvanizing is used more in Europe and America due to different specification demanded by manufacturers in those countries. Since Japan manufacturers prioritize paint adhesion, they use galvannealed.
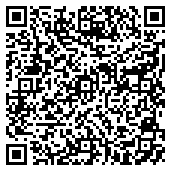
scan for download